Hydraulic Fracturing, Upgraded.
At ProFrac, we are more than a hydraulic fracturing service provider – we are your partner in well production optimization. Equipped with high-grade technology, we aim to optimize your operations with a realistic and responsible approach to reducing our carbon footprint.
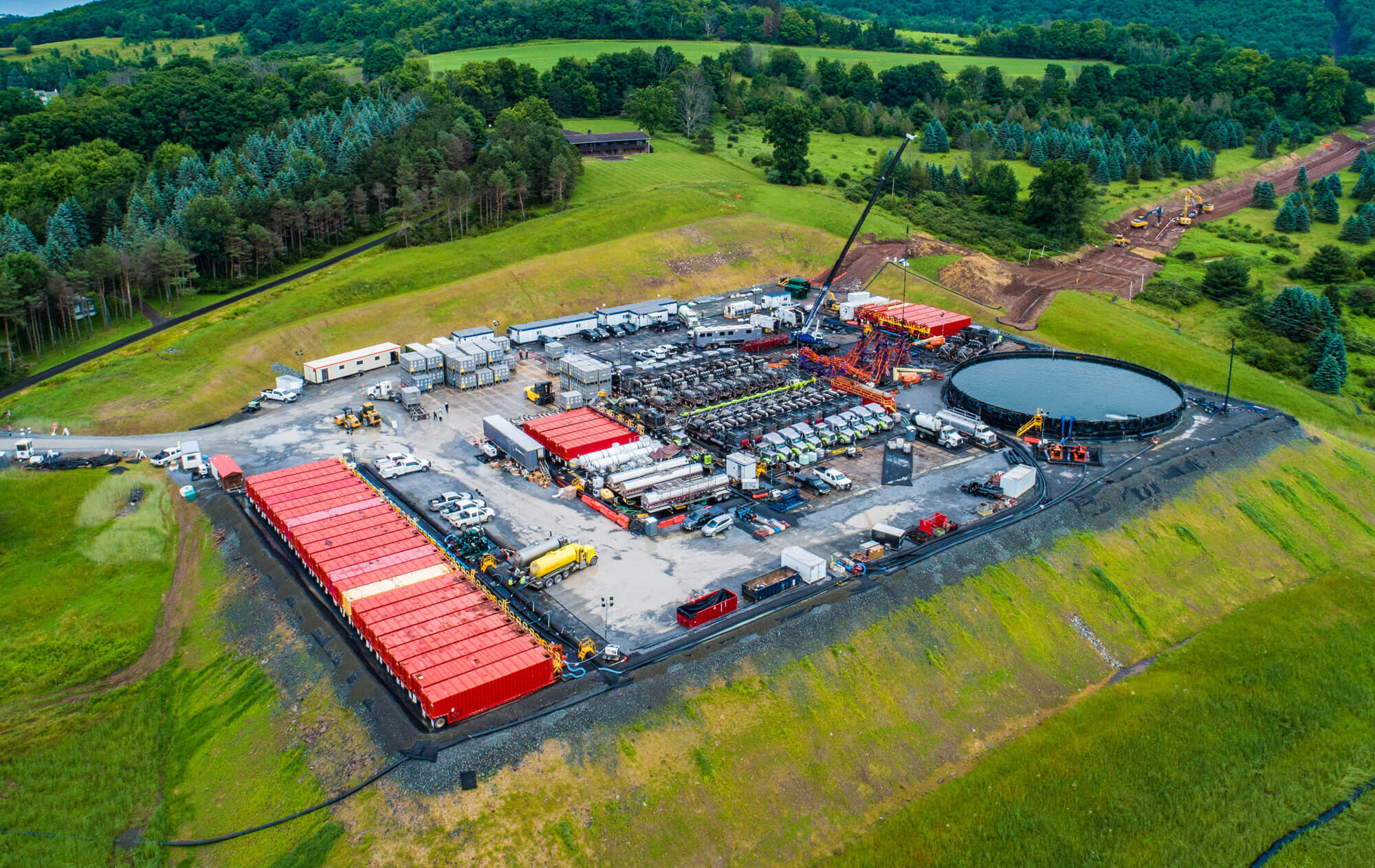
Why ProFrac
CO2 Mitigation
Our commitment to a cleaner future is ongoing. We adopt pragmatic strategies to mitigate carbon emissions.
Sustainability
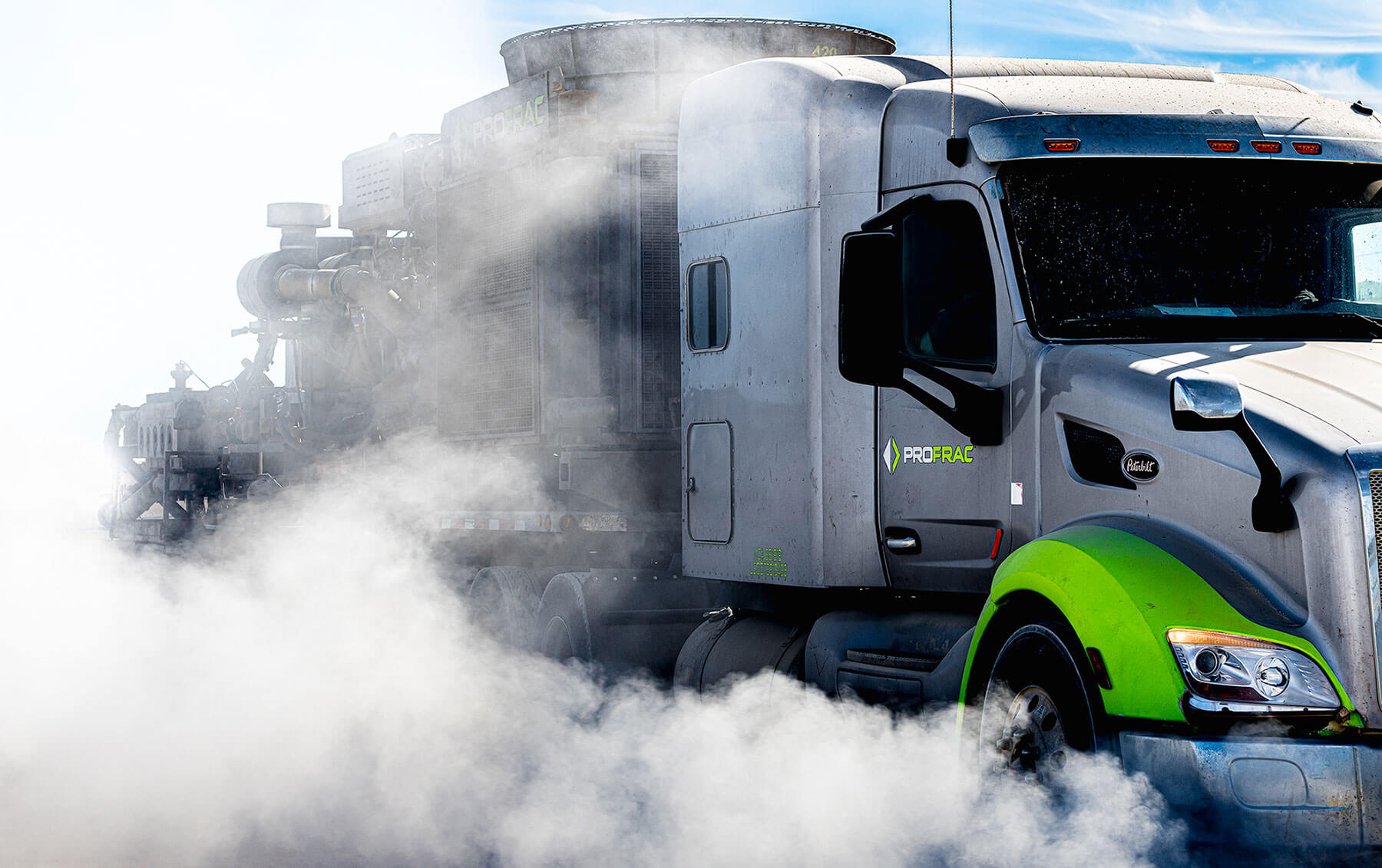
Why ProFrac
Operational Efficiency
We focus on substance, providing streamlined processes that emphasize measurable performance excellence and value delivery.
Services
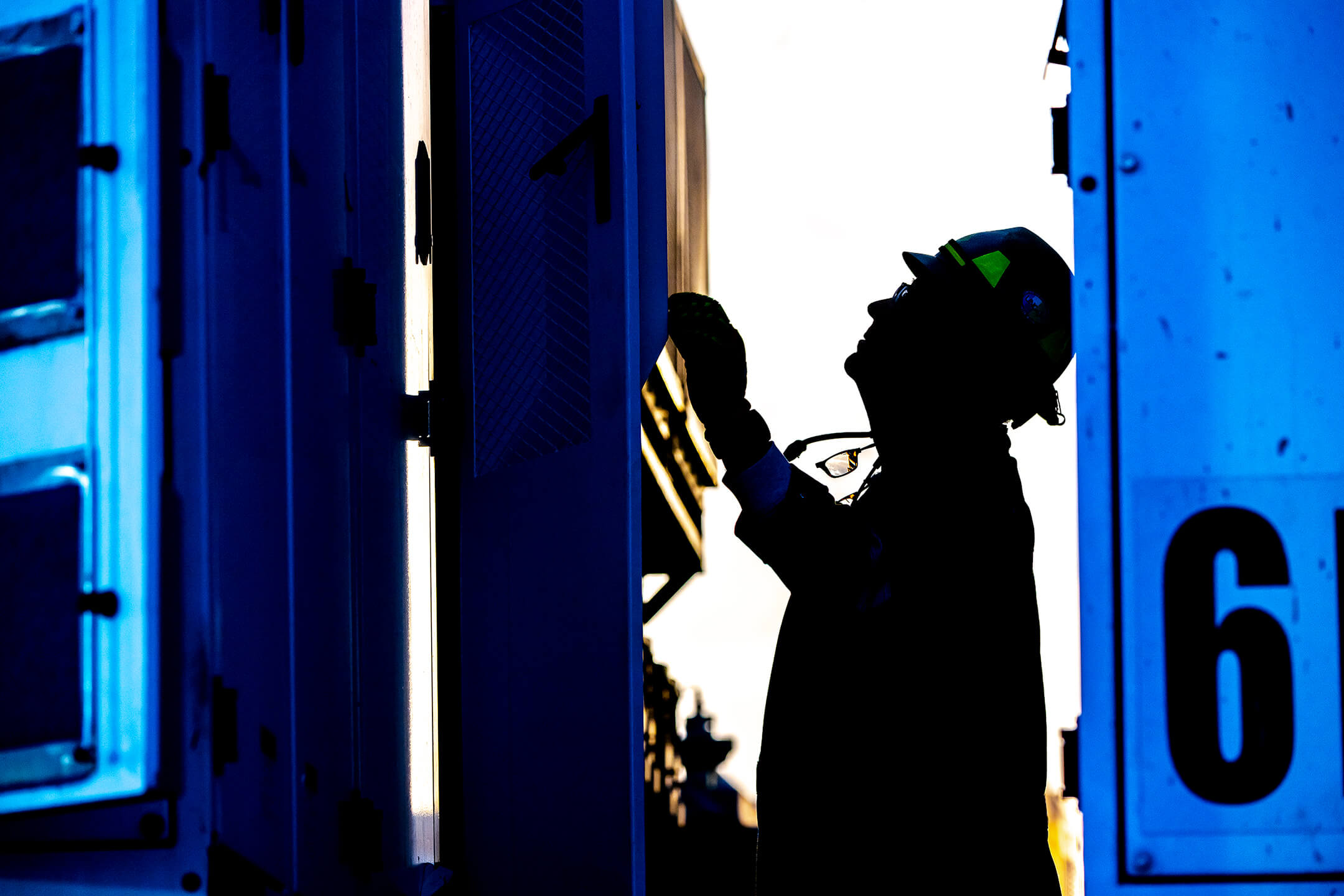
Why ProFrac
Cost Efficiency
Proven products and services that are not just cost-effective but also designed with a strategic edge for superior value.
Services
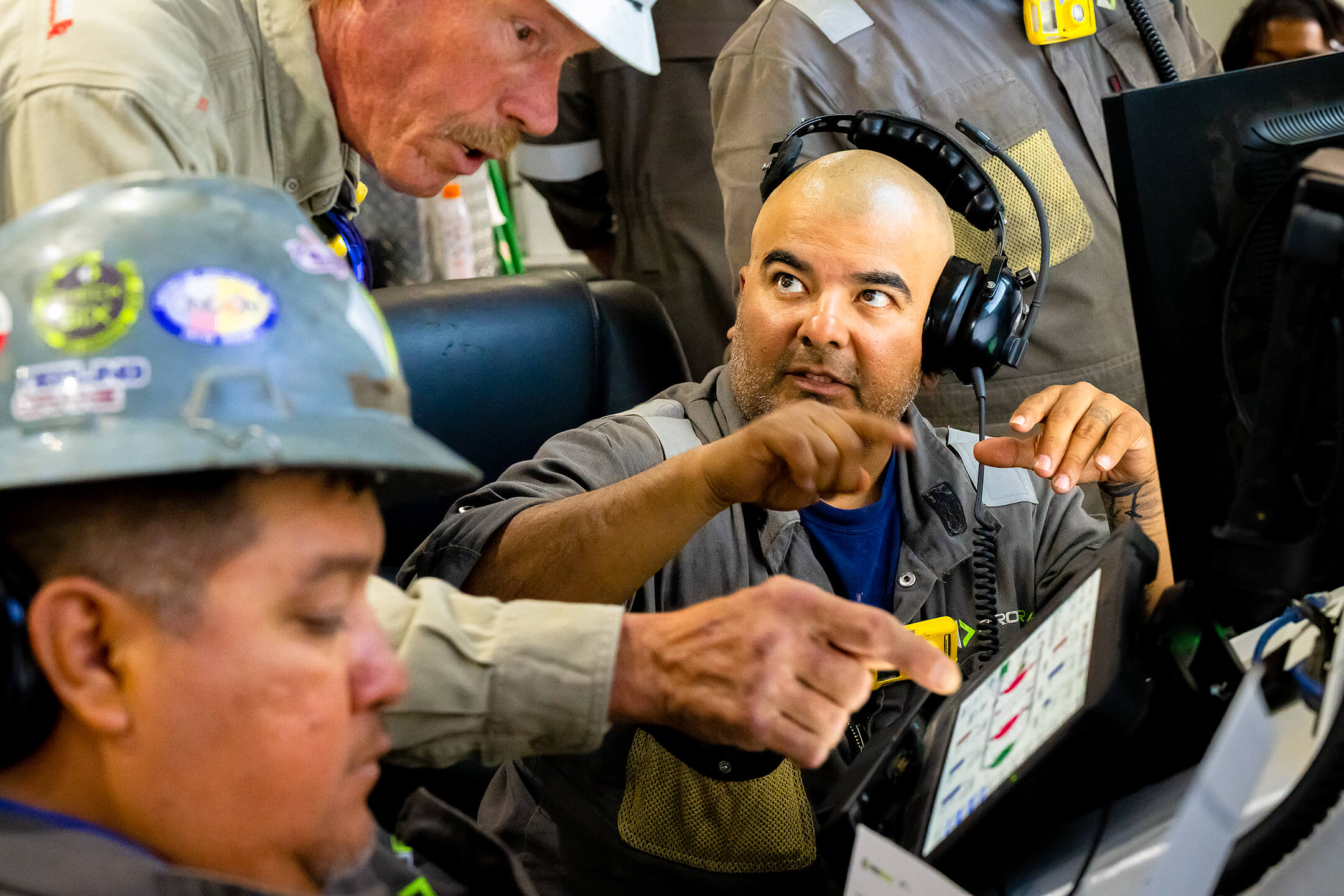
Why ProFrac
Customer Satisfaction
We build trust and create lasting relationships, prioritizing your satisfaction with a transparent and client-centered approach.
About Us
Full-service capabiliites
With state of the art advanced equipment, custom manufactured and maintained for superior efficiency, ProFrac is the leader in providing hydraulic fracturing services to maximize well productivity.